Welcome to my thesis presentation – Aggregated assemblies, Which talks about the revival and improvisation of indigenous construction practices through technological interventions in AEC
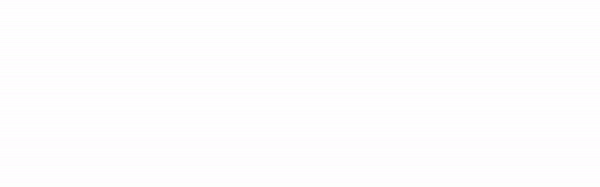
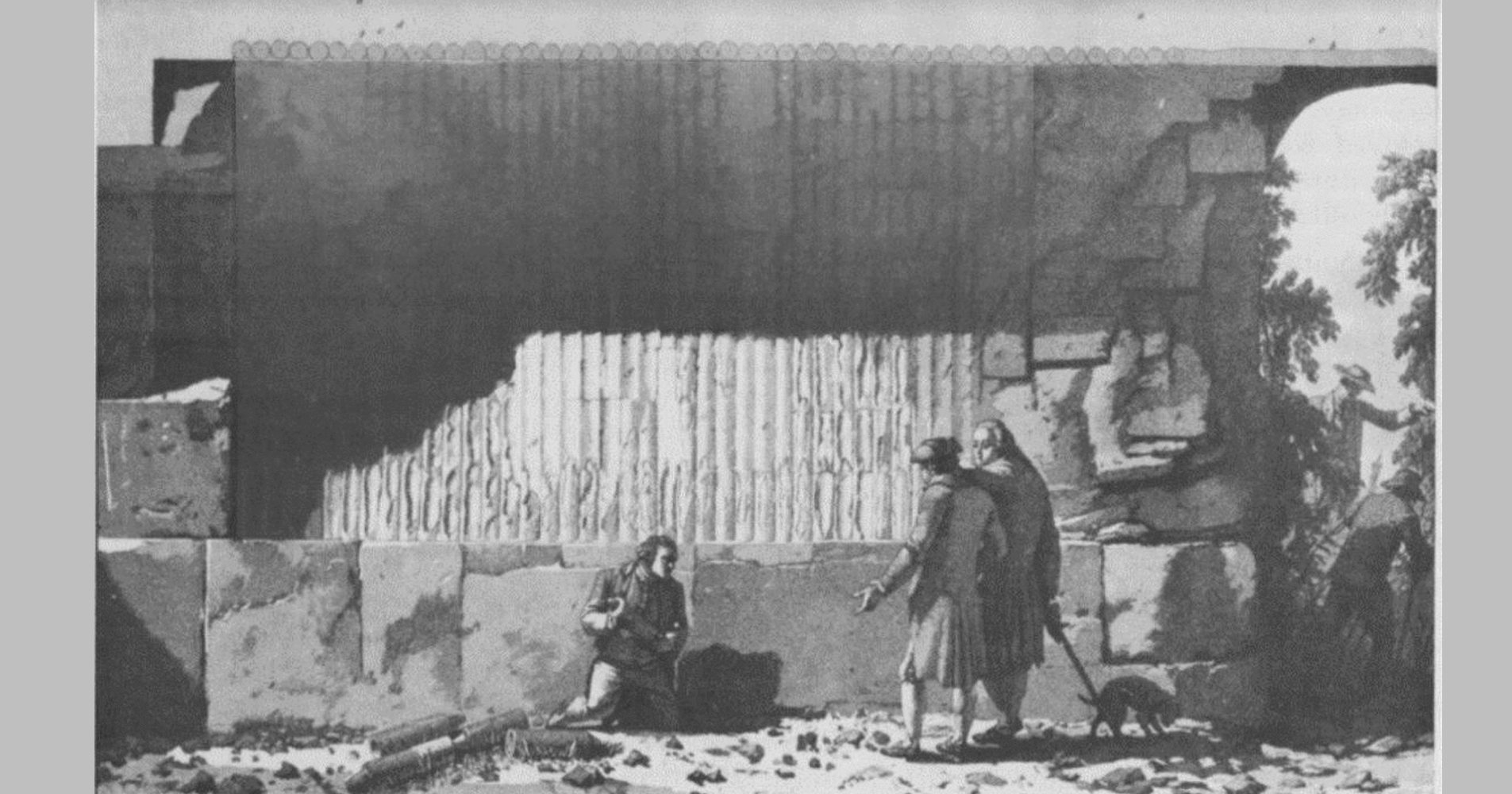
A question that comes to mind is Why should one look at indigenous building practices? What does it mean to give them more visibility? Indigenous techniques generally source local materials for the construction, come with inherent environmental performance benefits and hold a lot of socio-cultural value.
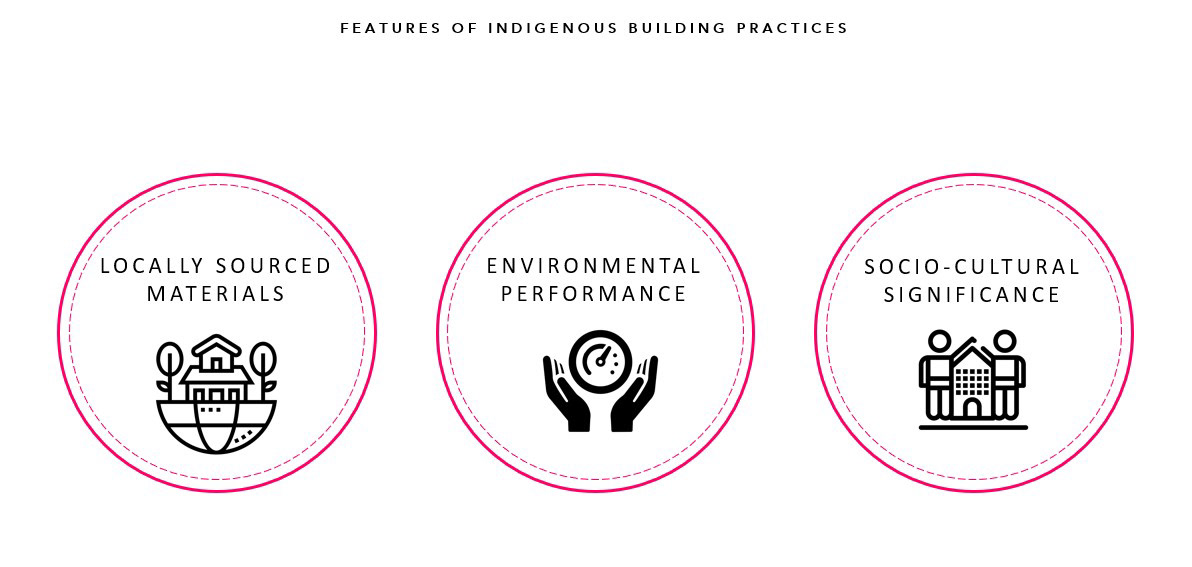
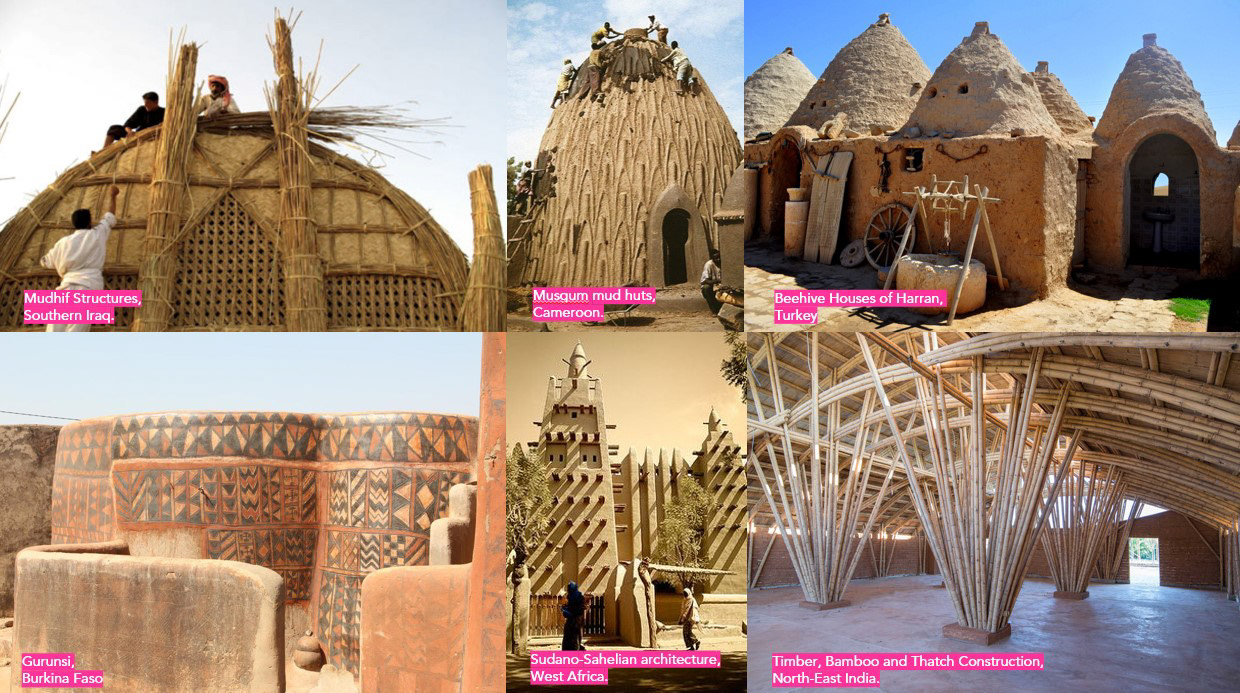
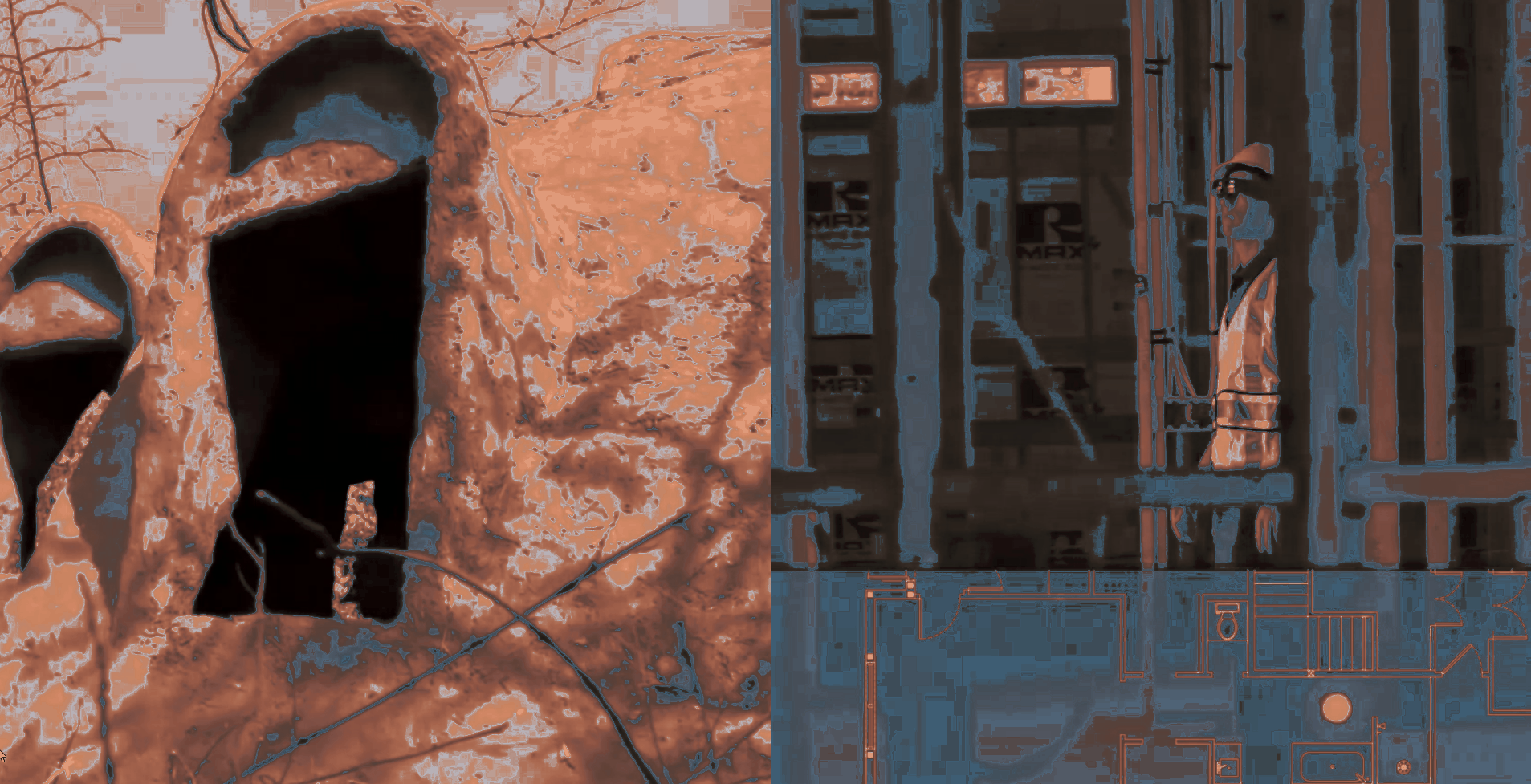
My project depends on what definition of technology I am basing my project on:
I see technology as helping something to come into being. A designer or craftsperson is not the ultimate source of the reality of what they are making - in fact they are someone who helps in this process of making. If we borrow from Heidegger, modern technology is often not seen as an aid for designing, but rather as something that is forced into this process of making.
Technology within the AEC industry addresses a limited array of techniques and only focuses on standard construction techniques that are replicated all over the world. Automation and standardized construction are greatly affecting the Learning and passing down of traditions and culture within indigenous communities which poses a great threat to their identity.
But it is also true that without the inclusion of technology, a craftsperson's impact remains limited wrt the things they can physically do- so how does one go about this inclusion, without having makers losing their roles?
So how do we combine the intelligence in indigenous practice with the current technology?
With this in mind, my project poses the following overarching questions:
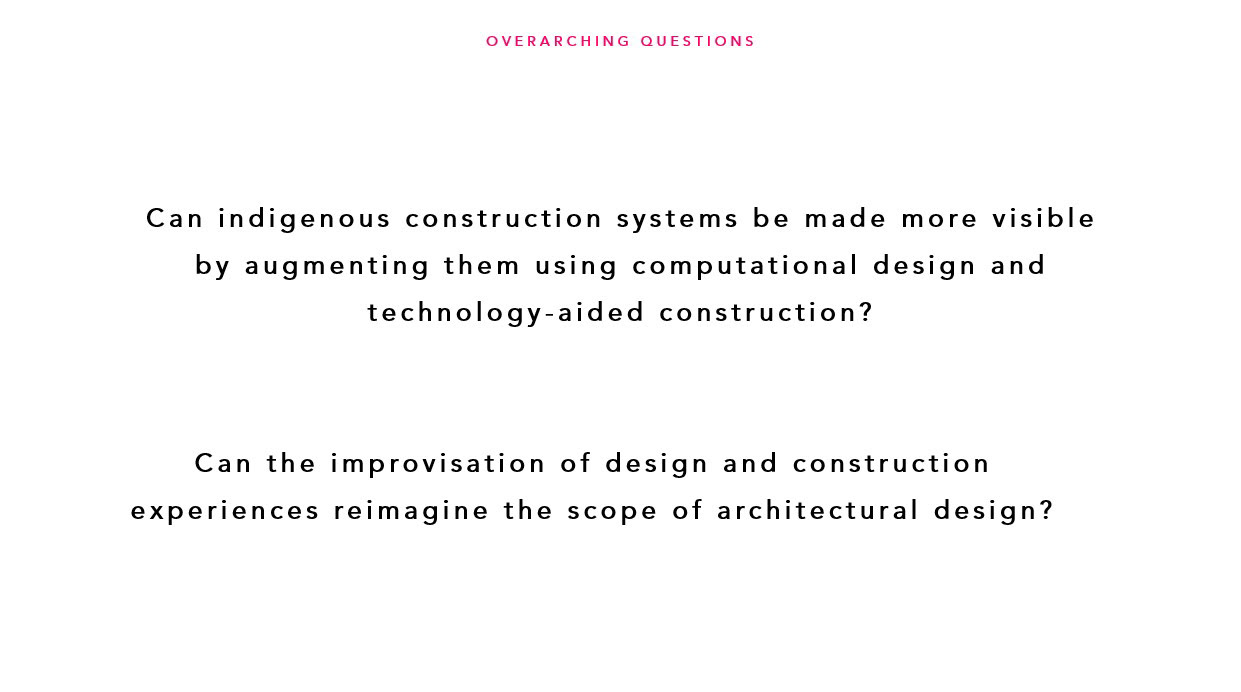
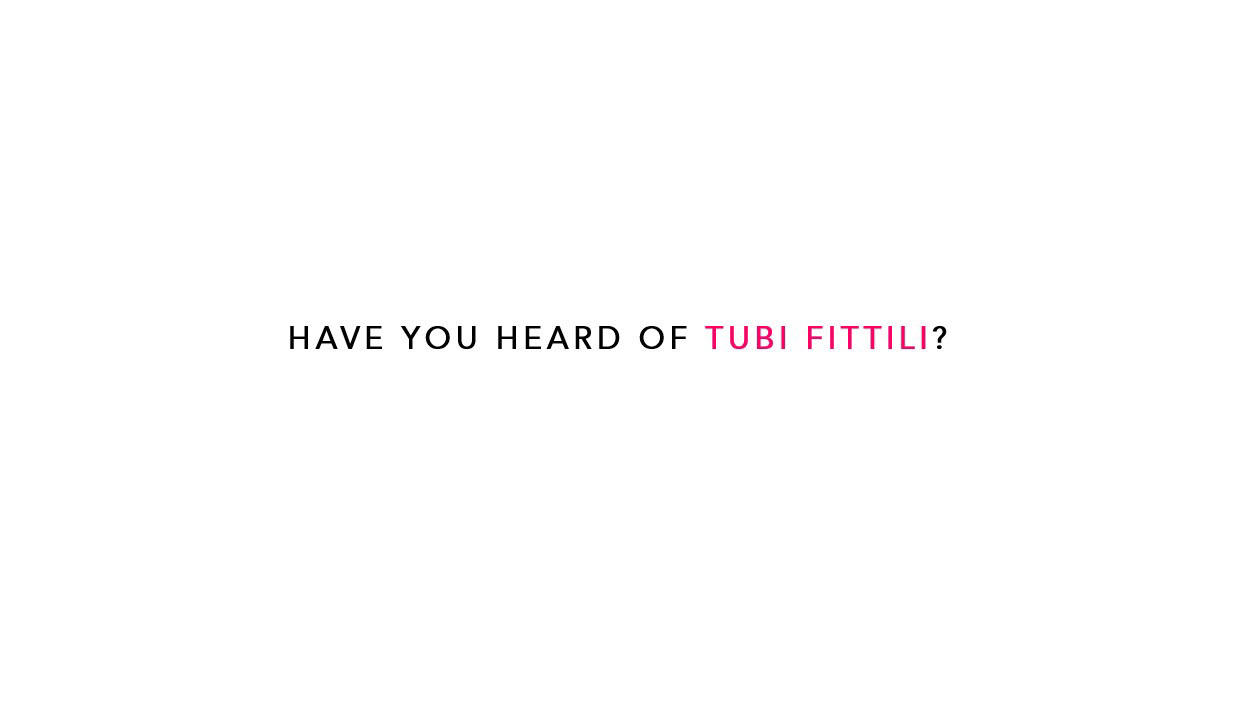
“Tubi-Fittili‘’, is a technique of tubular vaulting, which originated in the Roman empire and had gained popularity due to its ability to offer heat resistance and insulation, while ensuring a lightweight design. It is a building technology that was born as a response to the scarcity of timber for scaffolding and an immediate need to provide for the growing population. I repeat– “no scaffolding throughout its construction process. “
Each vault structure is comprised of standard individual terracotta tube modules that are cylindrical, and one end narrows to form a nozzle-like projection. This enables each tube to interlock perfectly with its neighbor. Any Geometric variation at the micro level - tube modules - greatly affects structural feasibility at the macro level - the vault structures. Generally, Grout is used to firmly position these modules in place or, the entire structure is plastered from underneath.
An interesting part is that according to a study that talks about terracotta vaulting with tubes, these modules are also among the first hollow bricks in history.
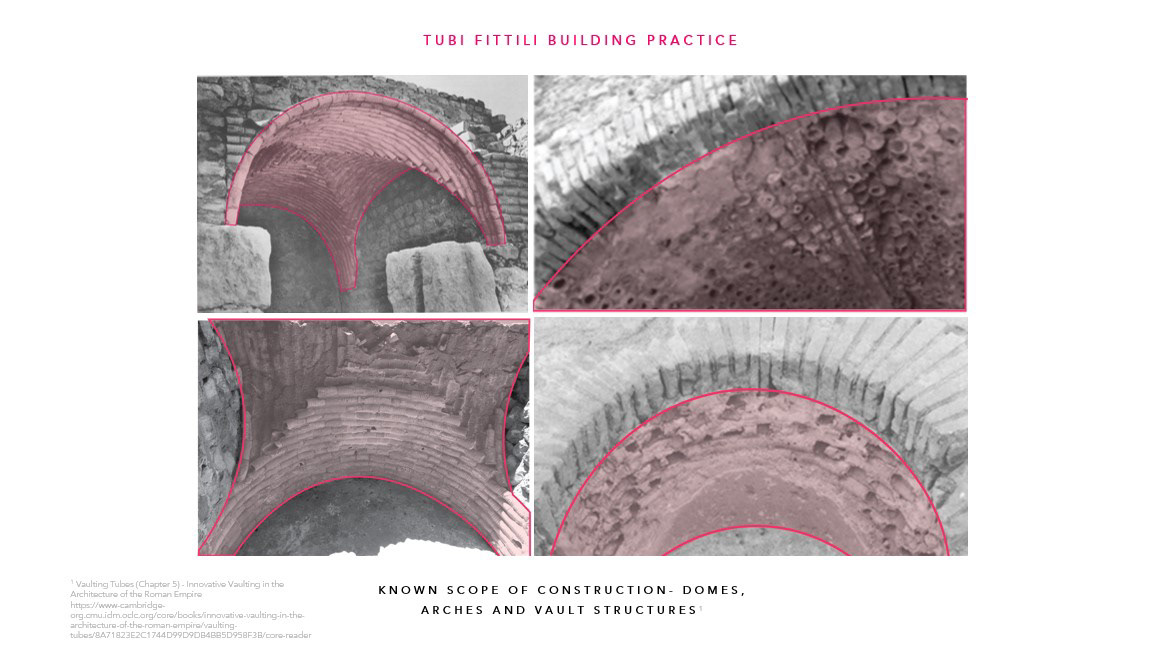
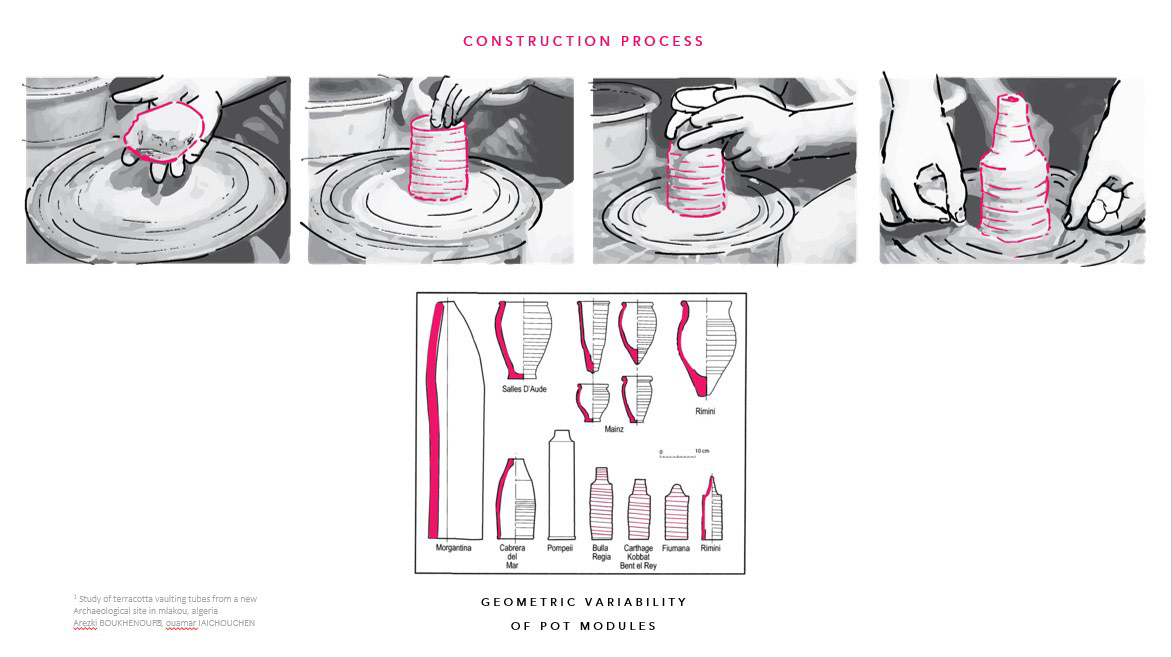
While standard brick construction relies on mortar and gravity to secure layers of bricks in position, tubi fittili involves the precise positioning of pots relative to one another such that it always builds towards informing the global form of the structure. The keystone – is a custom module that is hollow from both sides and holds subsequent courses In position.
It is an in-situ construction technique that observes a very typical structural family consisting of domes, vaults, and arches.
As standard construction modules started becoming more widely available, architects and designers chose to construct with them - as skilled labor with this background was only limitedly available - There were other nuances of working with this technique such as producing so many pots and custom keystones, etc.
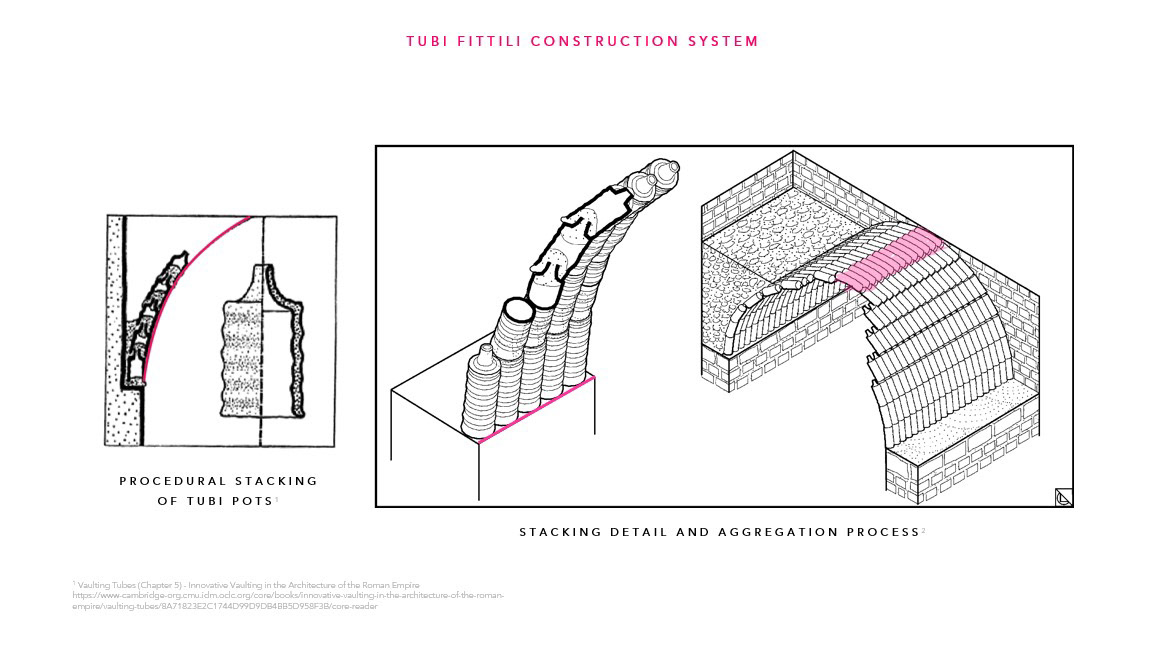
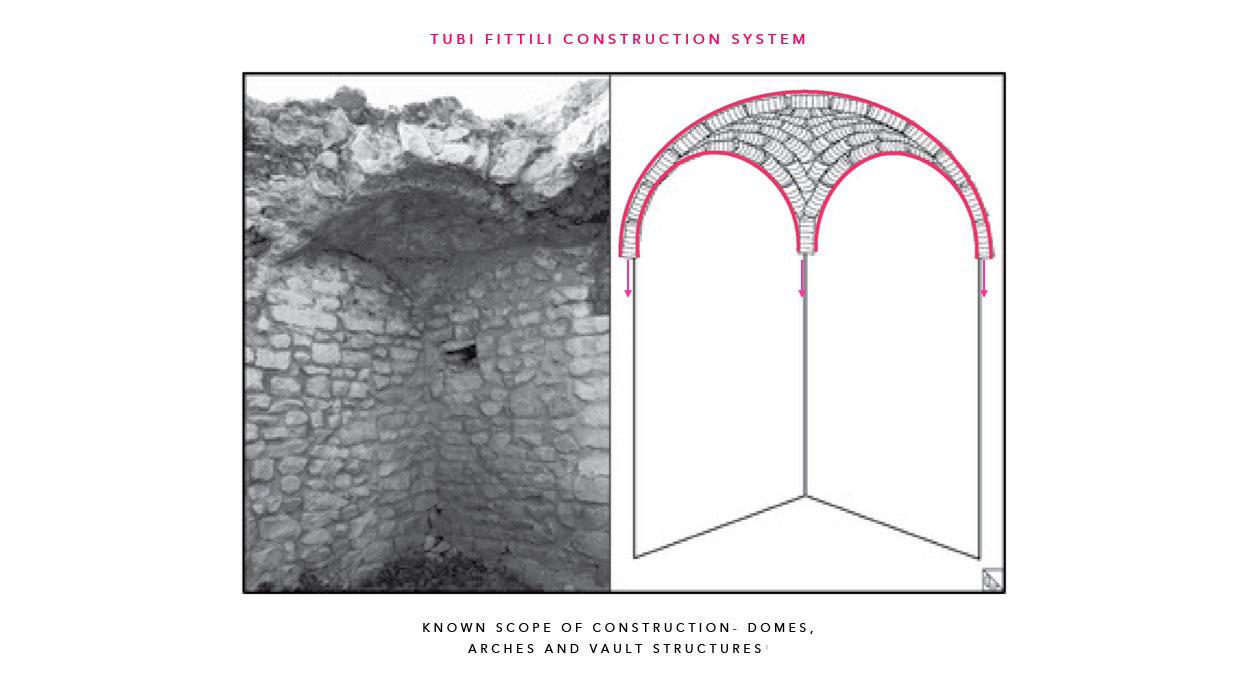
So to summarize the primary features of tubi fittili –we could consider the Modularity wrt to the use of these interlocking pot modules
Flexibility in terms of the arrangement of the modules based on the structure being designed – which changes with complex structures. And finally the precision or ability to nest or aggregate modules together with respect to one another.
So how does one use the current technology to best capture these primary characteristics?
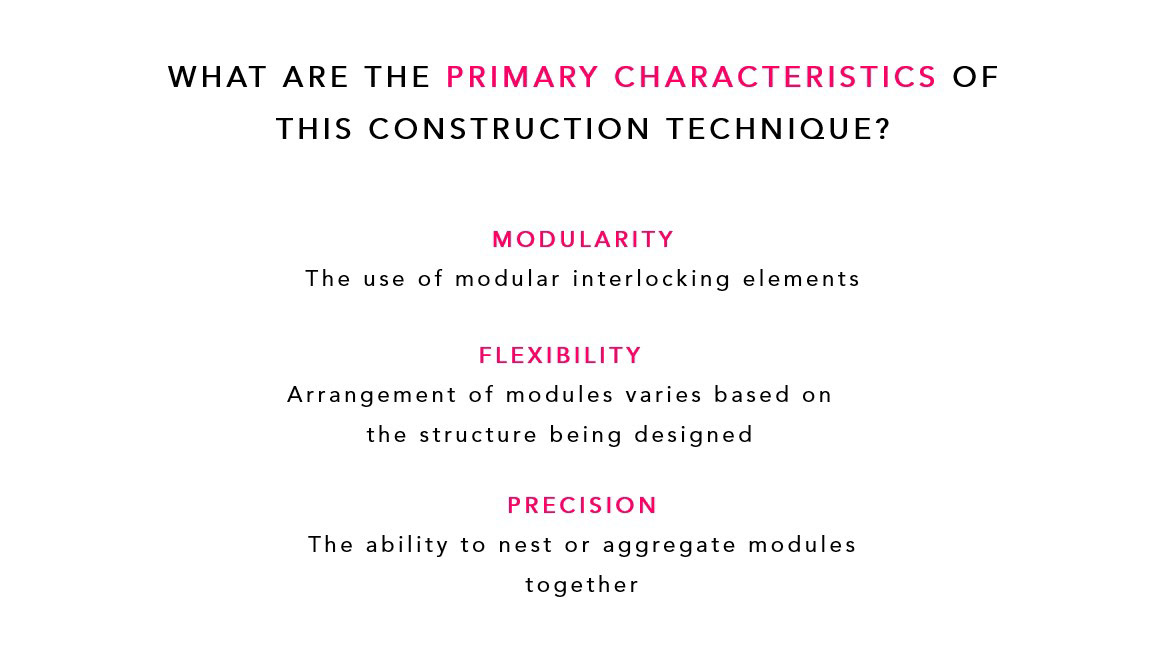
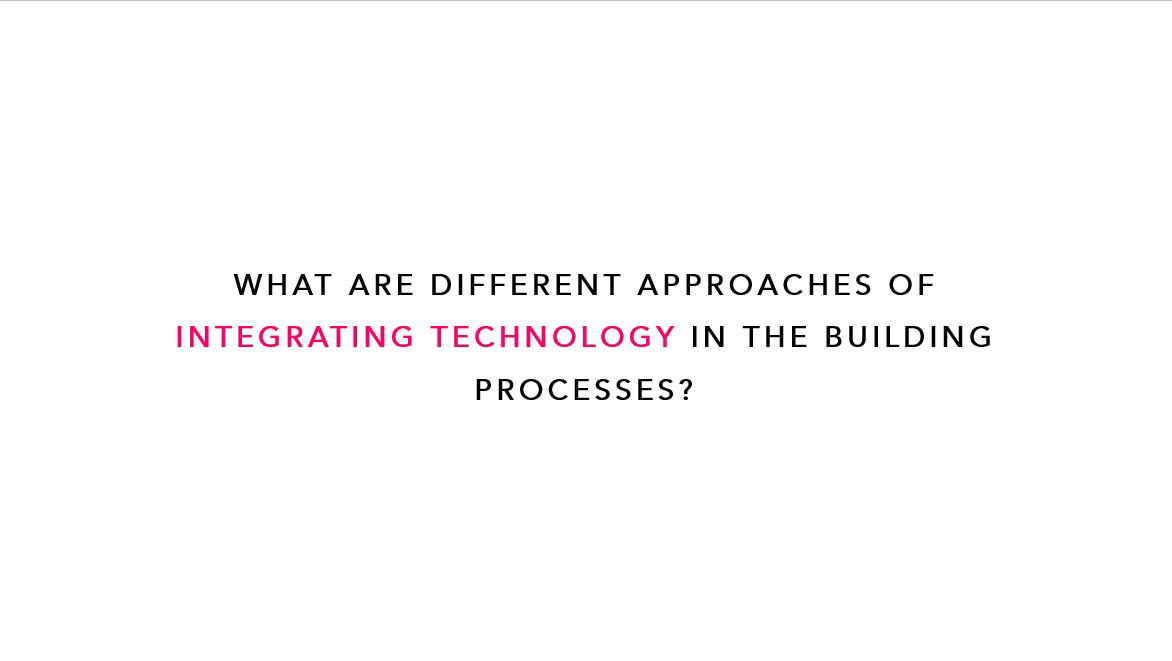
In the construction phase, Technology aided construction could have various outlooks depending on the scale, context, and availability of labor and resources.- and could vary from fully-automated scenarios to hybrid construction environments augmented manual construction would be Where technology is selectively used to assist the maker in the execution of relatively complex tasks.
All these scenarios do facilitate the construction of complex structures – in the first project by Grammazio and Kohler a robot is programmed to build a parametric brick wall, which is a rather complicated task when it comes to building manually - augmented bricklaying is another way that the task could be executed. This third project from ETH Zurich is a hybrid scenario where the human selectively jumps in the process of tasks that the robot is not programmed to do.
For the scope of this project as well as considering the current covid scenario, I would be looking at the augmented manual construction scenario.
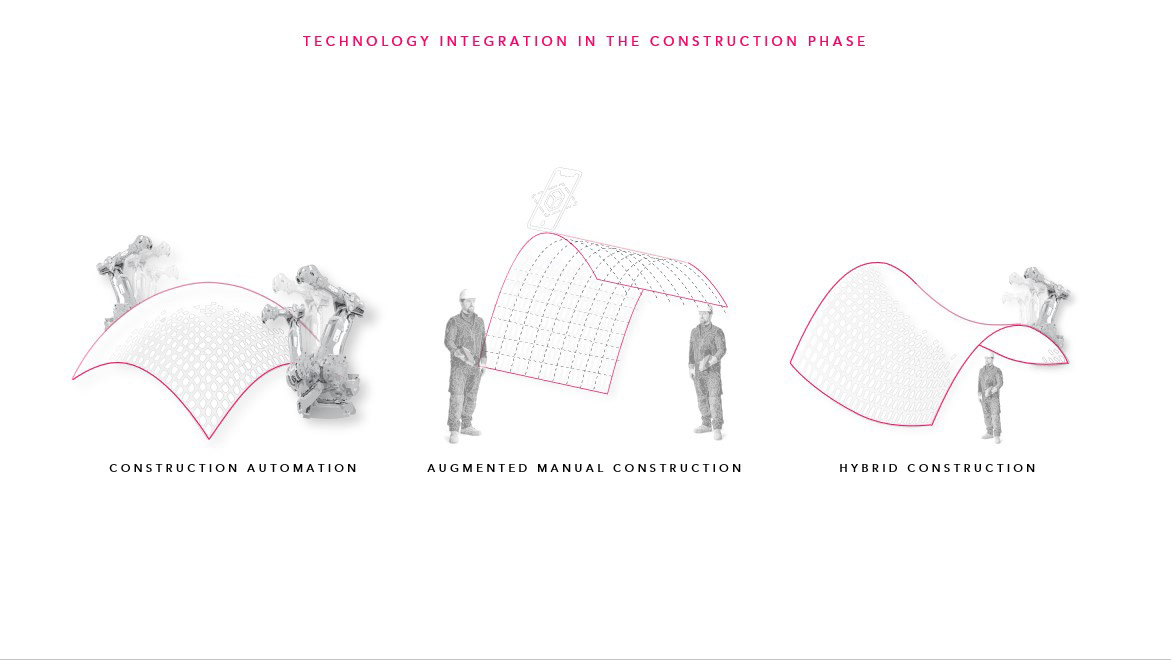
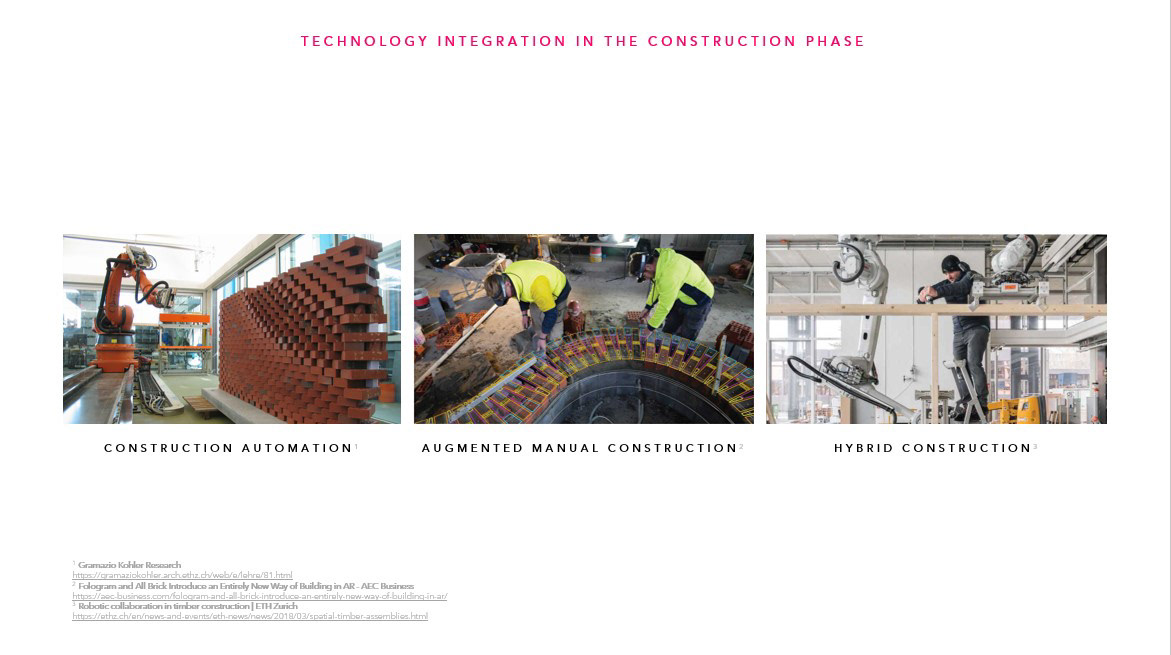
For the two parts of the project, I have been looking at ways in which construction workflows are rethought using computational design and fabrication tools. In this project that deals with Inca stone construction, Brandon Clifford’s studio: matter design looks at how current technology can be combined with the features of the Inca construction to create a new structure, comprised of repurposed stones.
Another project from Tongji University aims at creating vault structures using irregular foam blocks and talks about the incorporation of augmented reality and a human-computer collaborative framework to reduce accumulative errors that arise while working with the freeform building.
Building upon these precedents, how does one choose the right platforms and tools for digitizing Tubi Fittili?
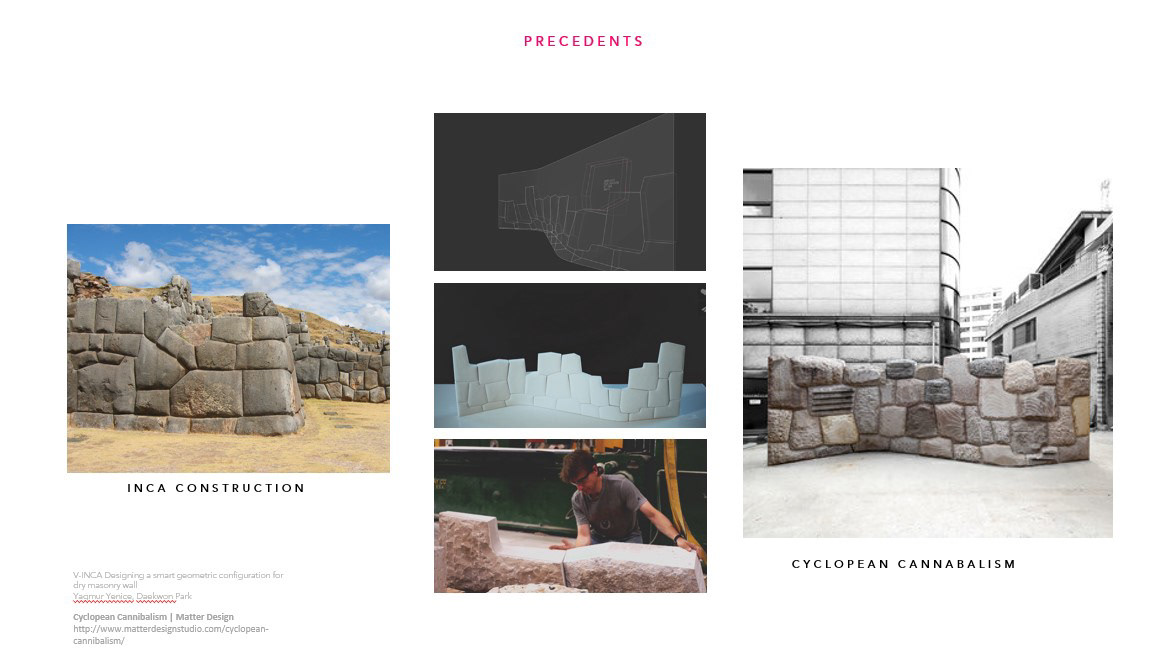
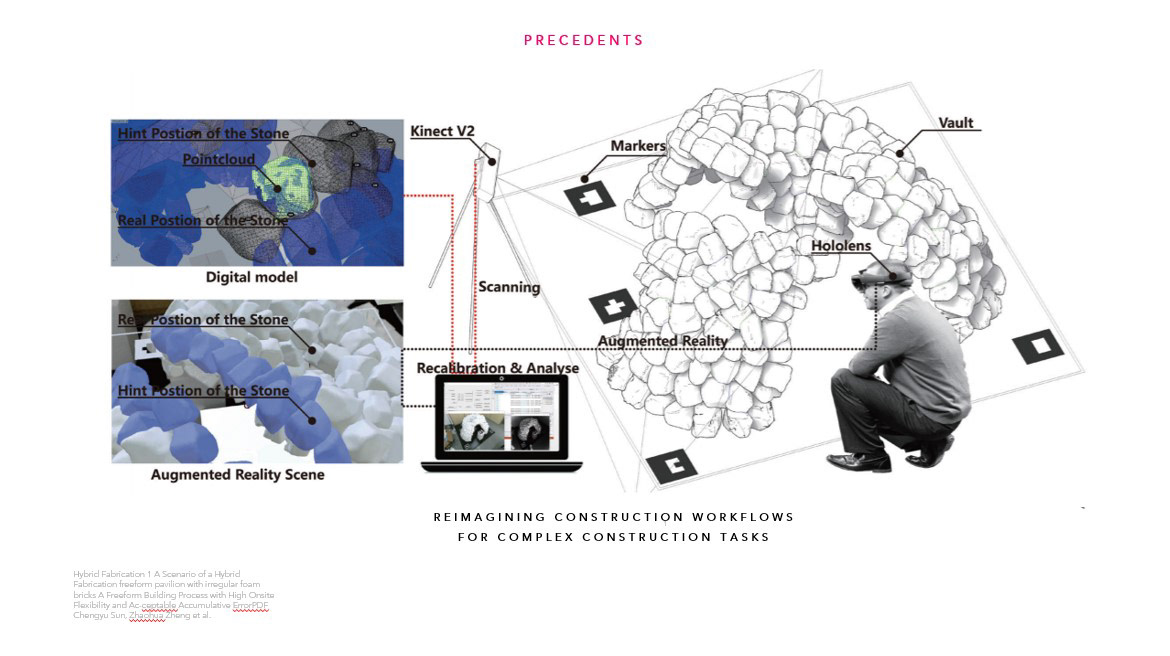
Let's have a look at the computational backed: Back when the Romans built structures using Tubi fittili, they for sure did not pass on working drawings to masons for construction, as technique relies highly on tacit skills and intuition of these skilled craftspeople.
But that’s not the situation now – and there needs to be a tool for architects and designers for being able to design using this technique in the current scenario
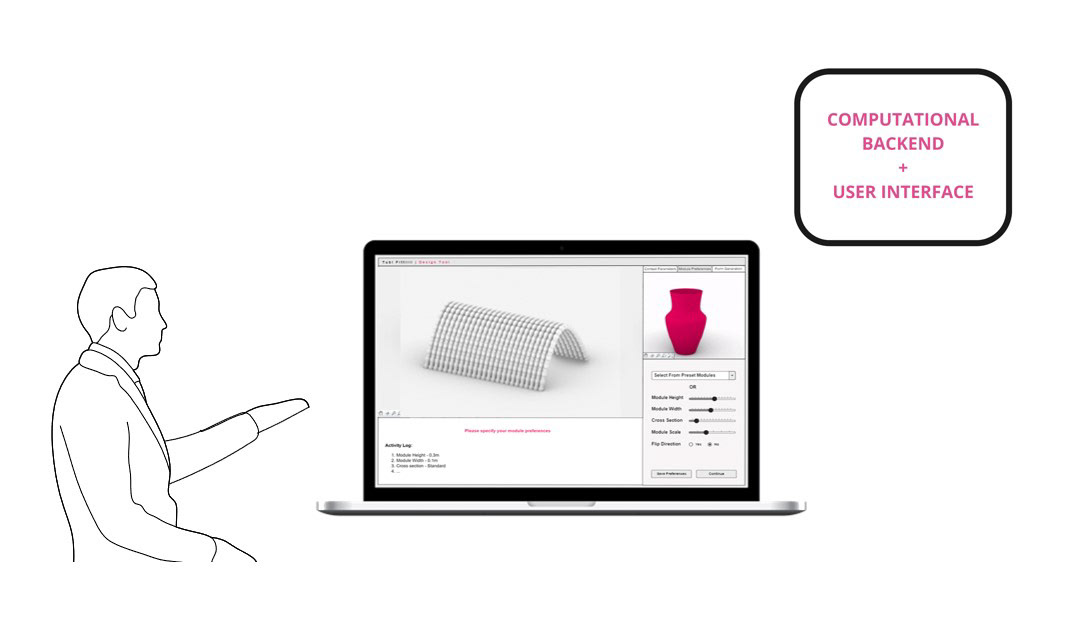
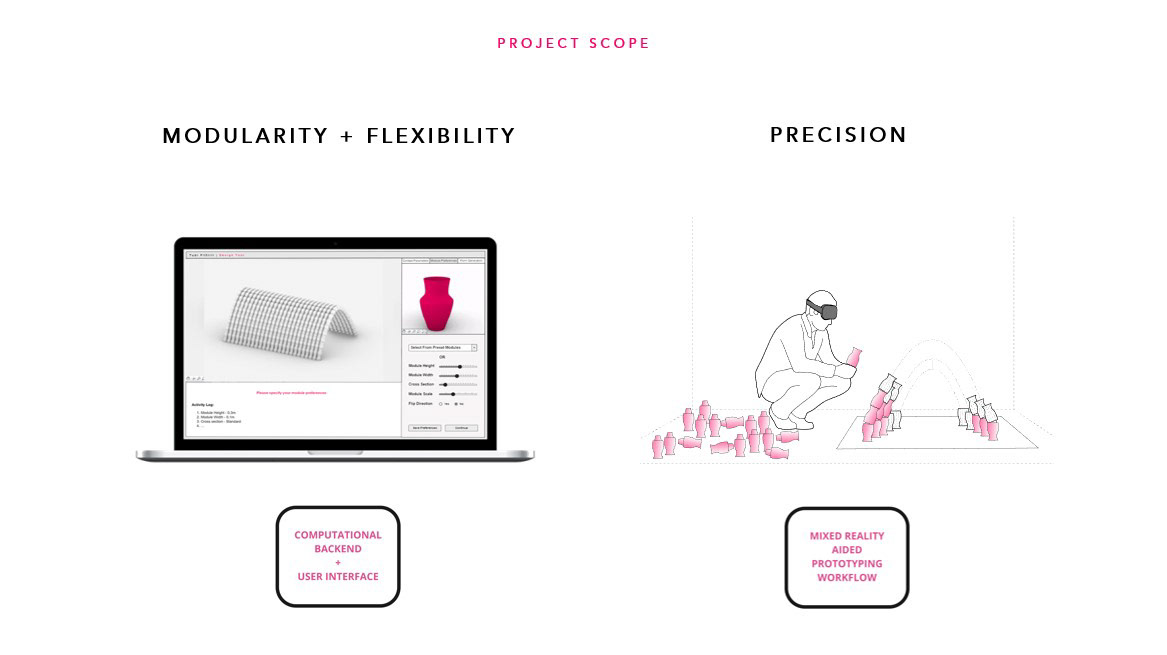
The methodology comprises deriving the component and structure details from literature and building upon them to set up the design parameters in the design environment that is built on top of rhino and grasshopper. Custom features pertaining to tubi fittili are added using grasshopper as well as scripting in python. Finally, an intuitive user interface is built on human UI, a plugin for grasshopper.
The structure designed is then brought in another platform on unity which enables the mixed reality aided workflow to be deployed using the hardware oculus rift and zed mini - which aid the maker in prototyping the structure designed.
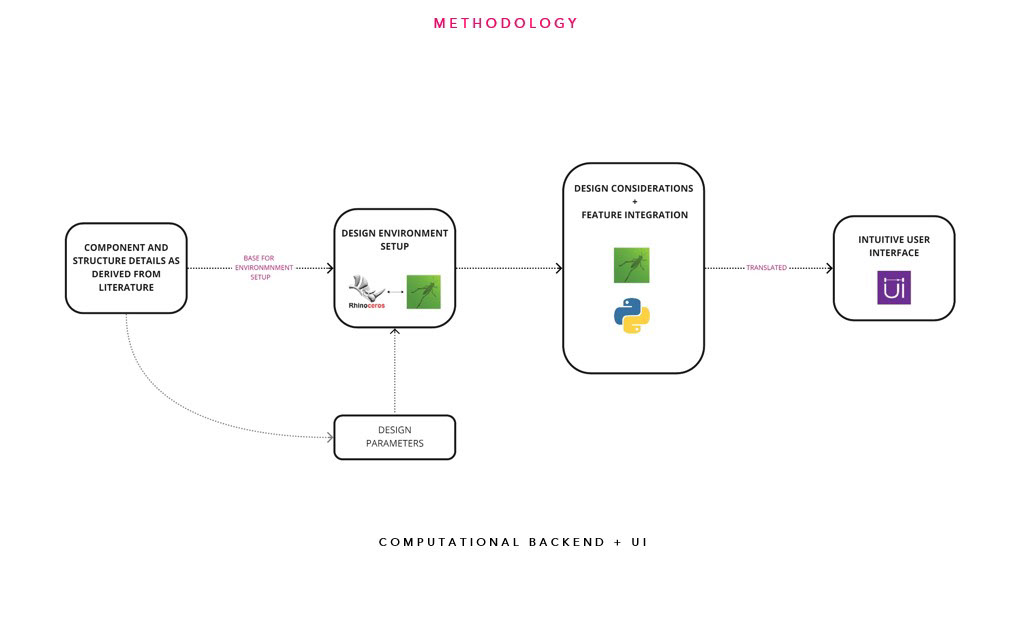
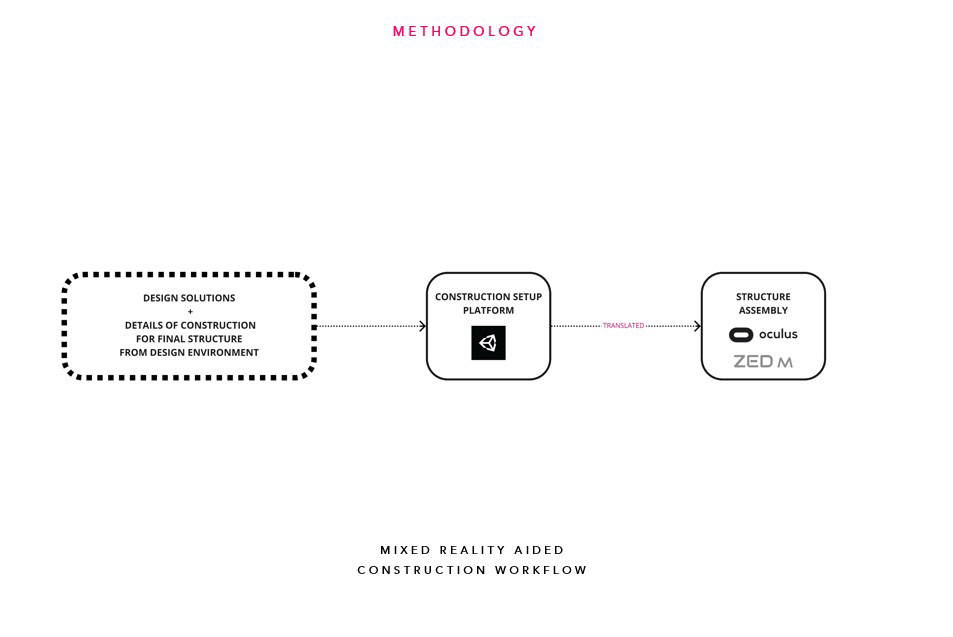
The design consideration occurs at three main stages- definition of design context, definitions of component details, and setting the constraints and goals of the final structure. ( spend some time on the slide)
A combination of parameters defines the features included in the final structure. These could be user-defined - such as the drive surface, the module preferences, etc or system automated - meaning the user would have less or no control over parameters – which could be parameters that measure performance and hybrid which means the user would have limited options to choose from, as defined by the tool.
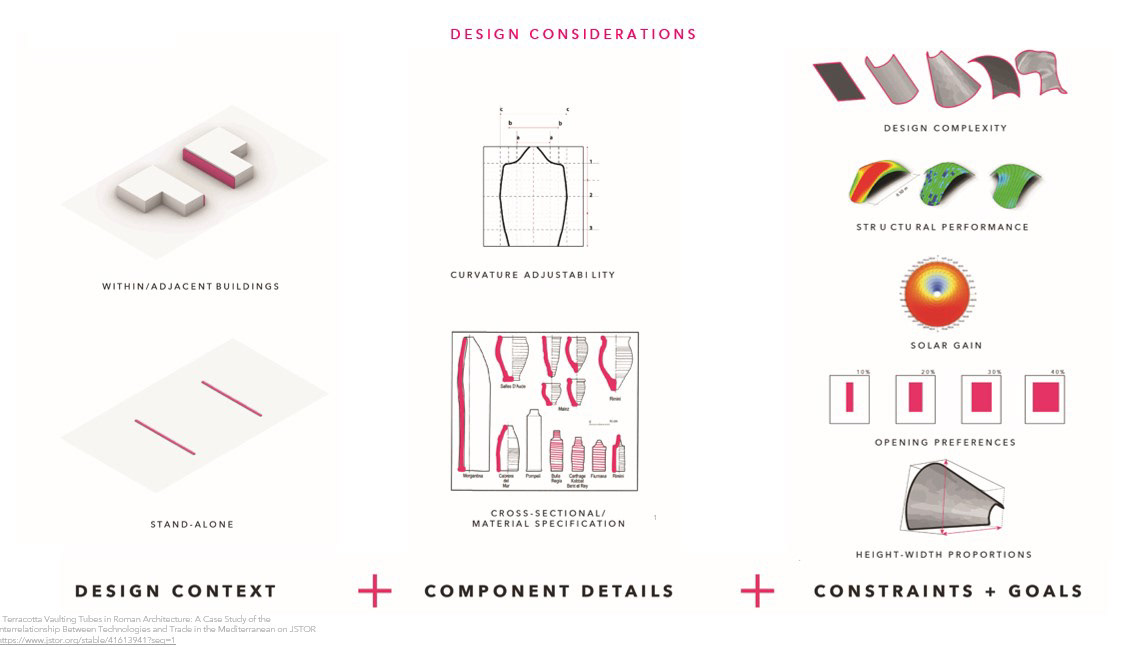
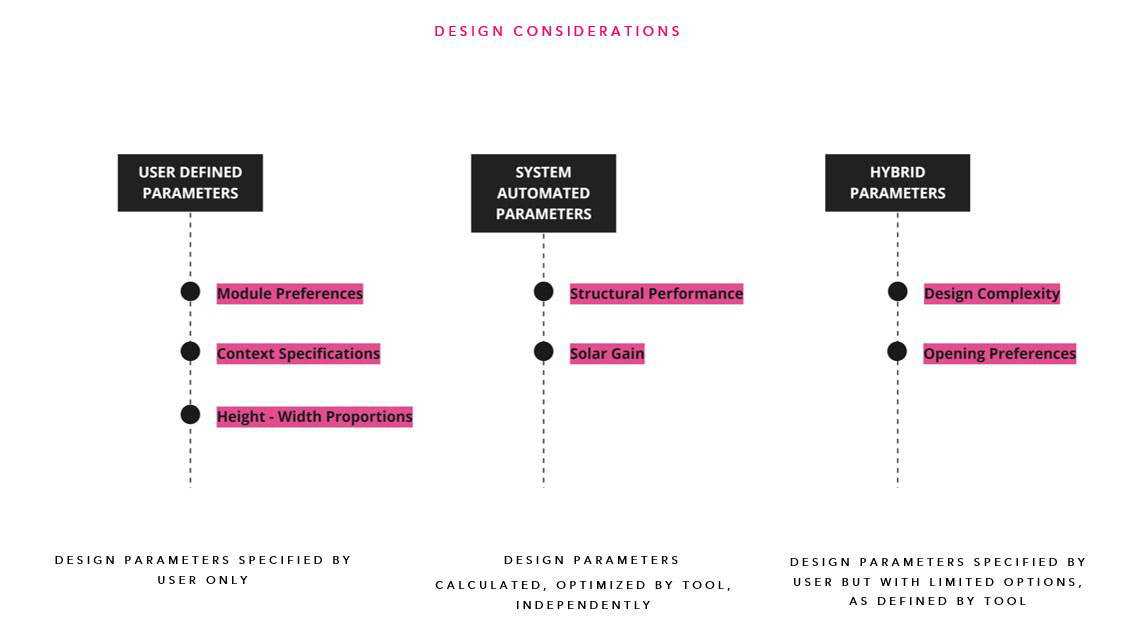
The algorithmic breakdown of this problem involved identifying the quantifiable features and limitations involved in working with this technique. This includes understanding the range of aggregation of modules, and their limitations with respect to the maximum and minimum angles at which they can aggregate.
Building upon the same approach (click mouse), with every aggregation the range of the module changes, relative to the previous module placed.
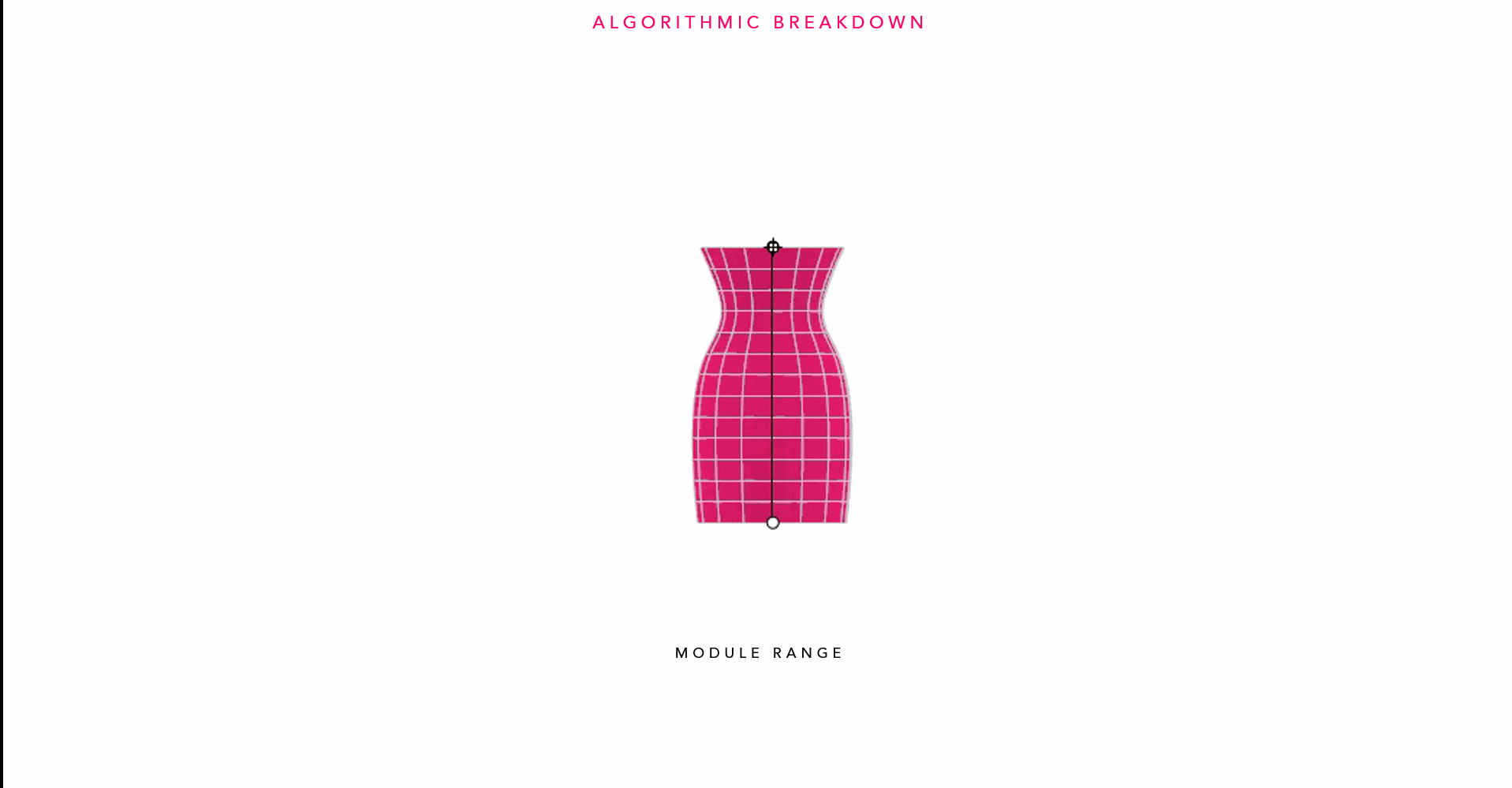
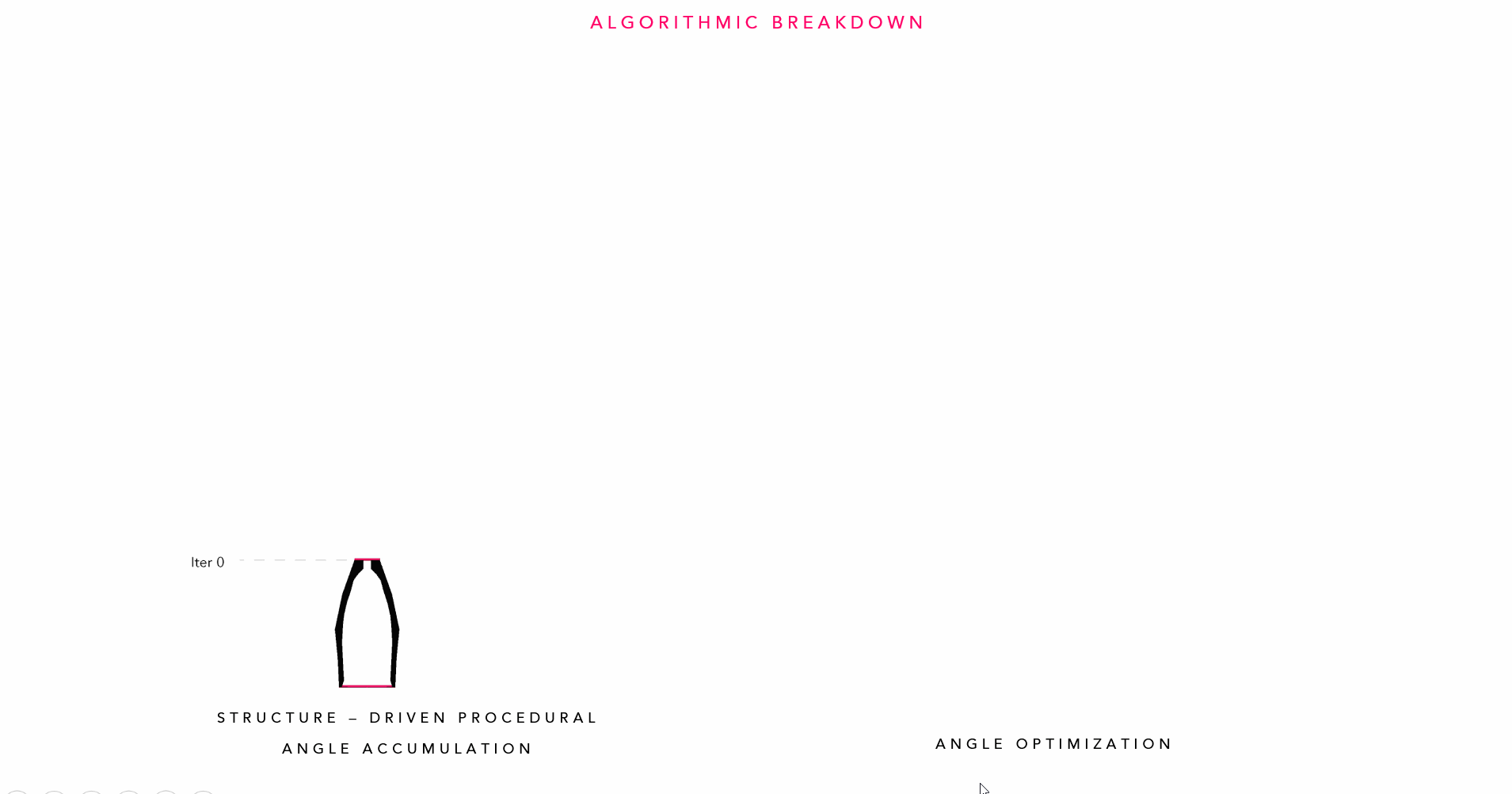
Now with this algorithmic logic, there could be two design approaches – the bottom-up approach which starts with the selection of module at the micro-level, which is followed by geometry aggregation to form the final structure or the top-down approach that start with a user-defined macro surface over which the aggregation takes place. Let's look at my attempt at the bottom-up approach.
I started by defining the details for pot modules and used an Agent-based modelling approach for geometry aggregation. This resulted in global structures that did not seem to work perfectly well with this system PLUS the user did not have significant control over the kind of geometries produced, AND nor is the system parametric. This process is stochastic in nature, and not deterministic.
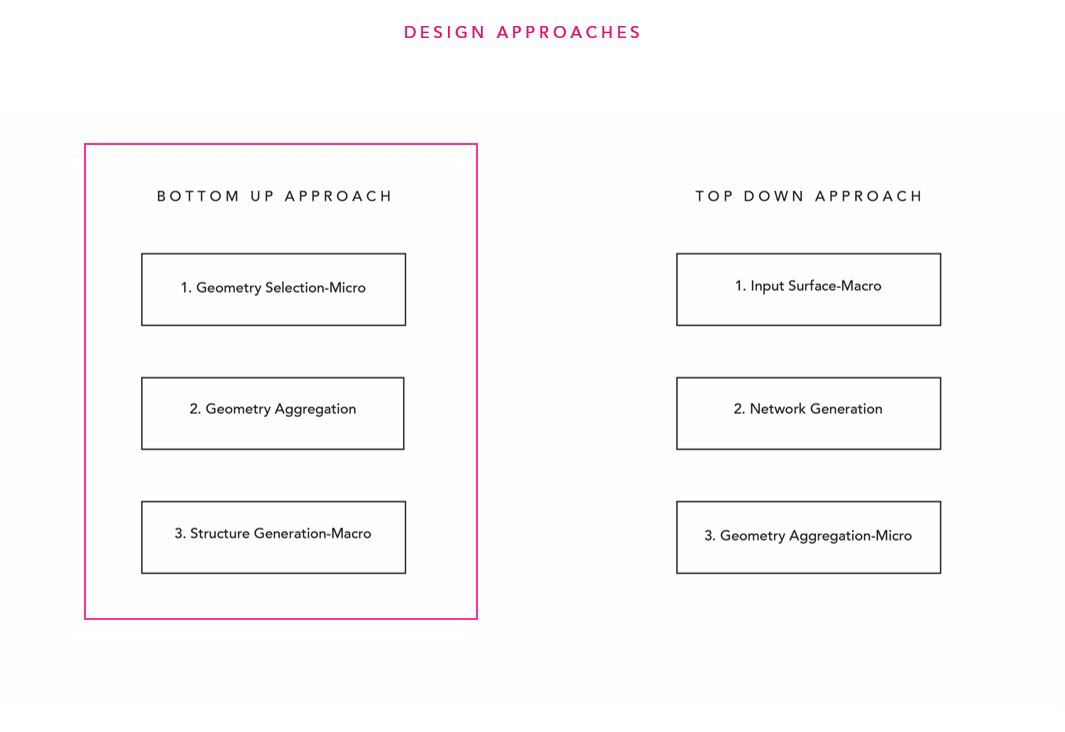
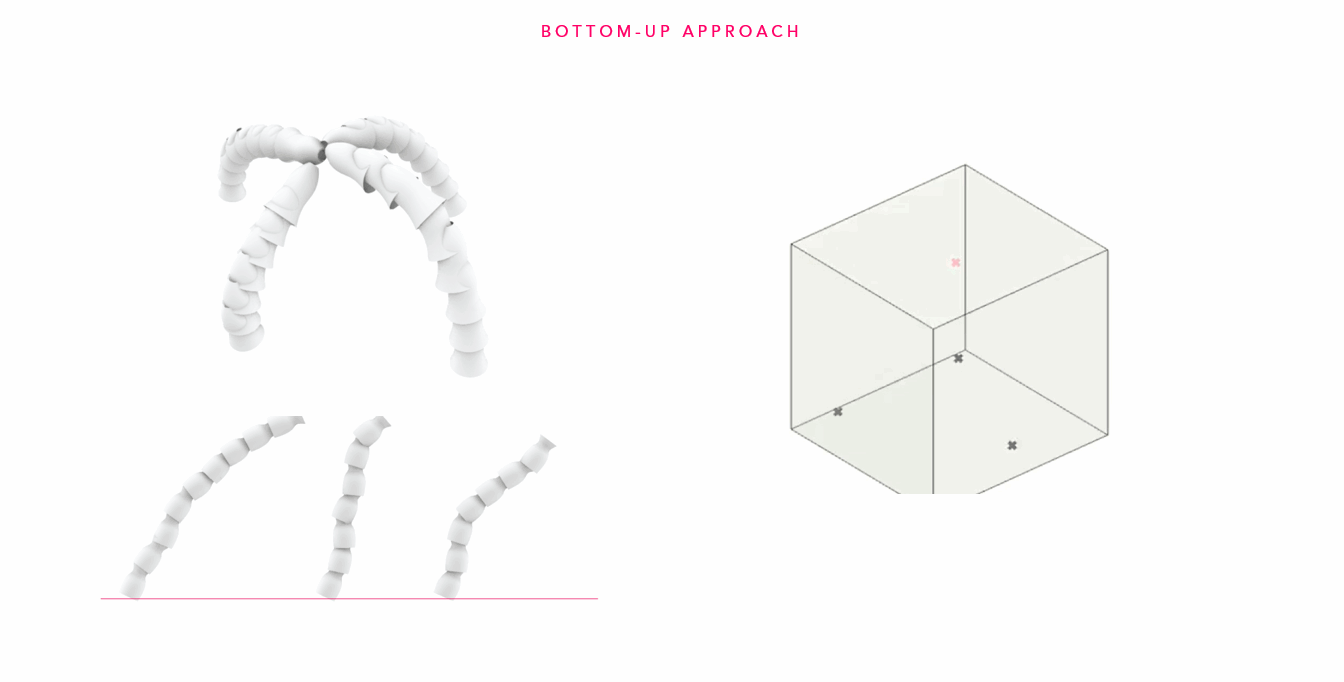
Because of these reasons, I started looking at the top-down approach where the designer defines the macro surface and has parametric control over custom features of the overall structure.
Based on the features of modularity and flexibility that need to facilitate, the design workflow consists of 3 phases
The first part includes the user having to upload a surface geometry which would be the macro-level form of the structure. The user has the ability to control the properties of this surface. This phase also involves the surface subdivision of the structure and the ability to control the seams thus produced. The next part is the custom module definition which parametrically informs the aggregation on a structural level. The last phase involves the definition of apertures based on either pattern generated during aggregation but also can cater to custom openings that require uploading an extra seam on the surface. Gaps in sparsely aggregated structures can be reduced by populating with more pots based on the same algorithmic logic. Once the user is satisfied, he could export this structure to be further worked within the prototyping workflow.
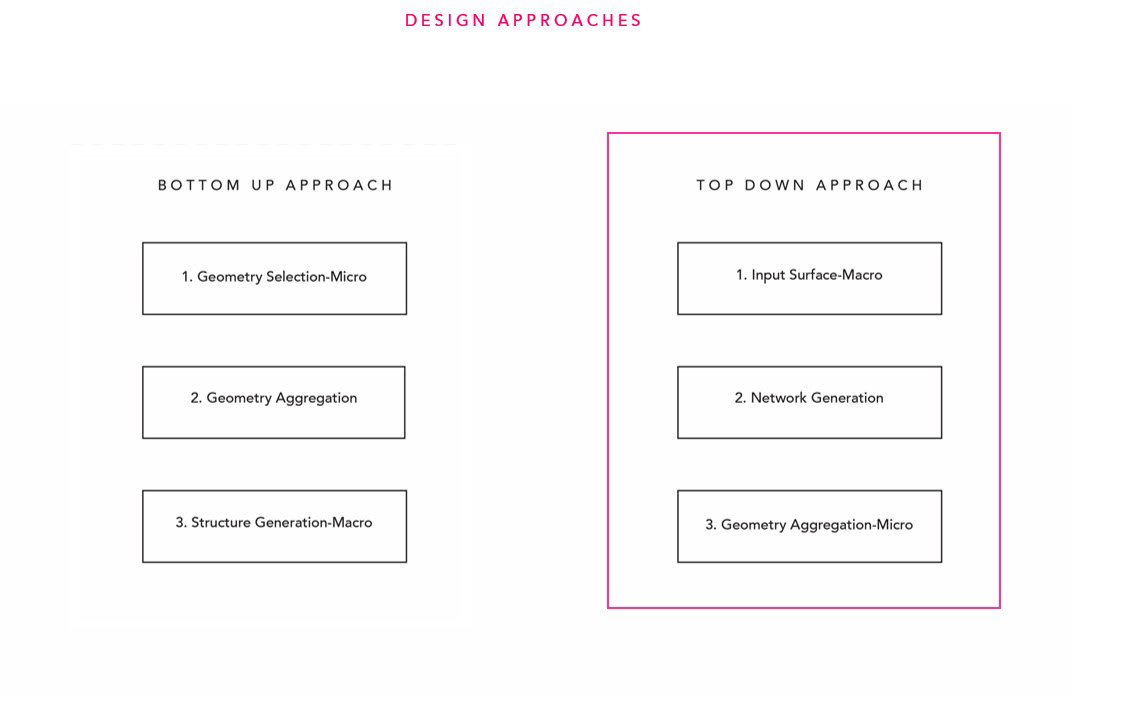
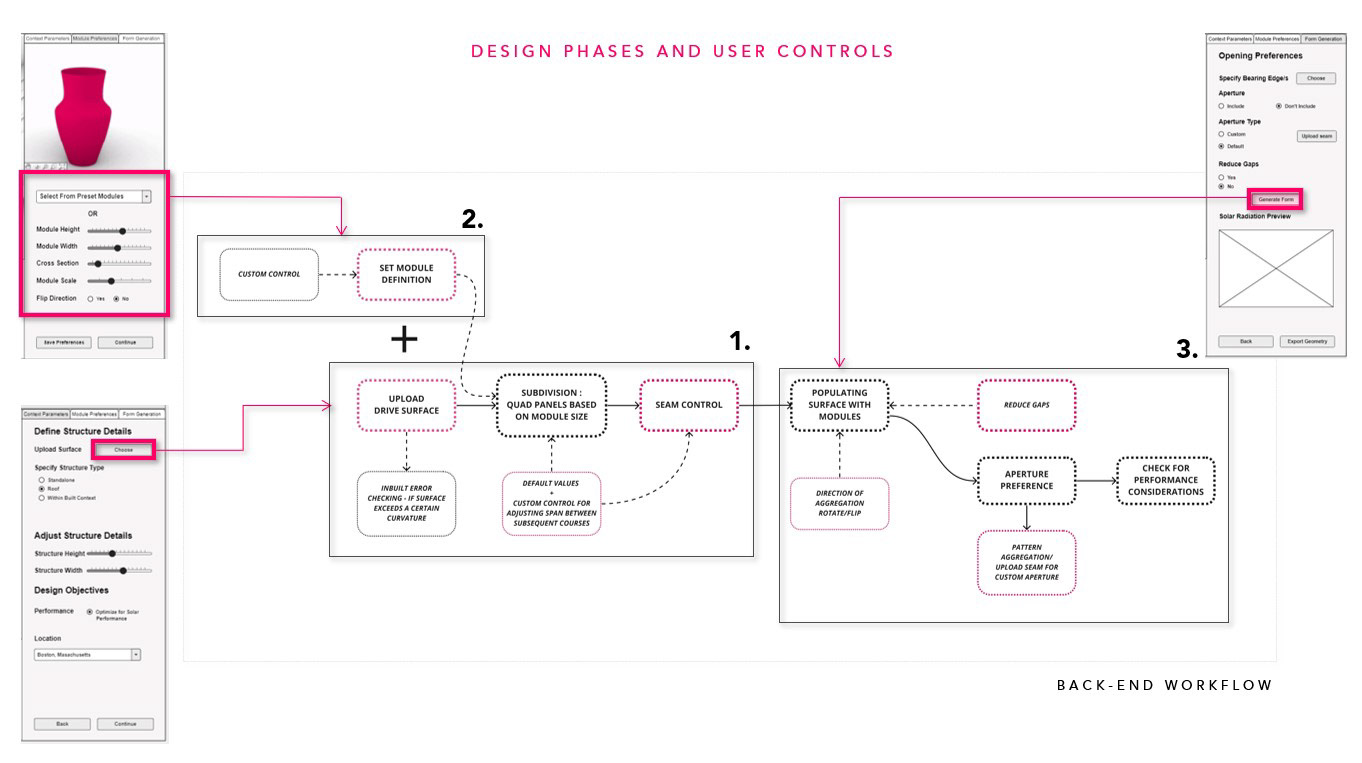
Here is a visual representation of the workflow in the first phase where the structure is uploaded, subdivided further, and then aggregated. It is also worth noting that the subdivision for all surfaces works differently – as seen in the case of domes with radial subdivisions and vaults with quadrangular.
Custom seam control – useful when a complex surface is comprised of several sub-parts (as seen in the precedent on the left) –where each surface may require a separate direction for aggregation
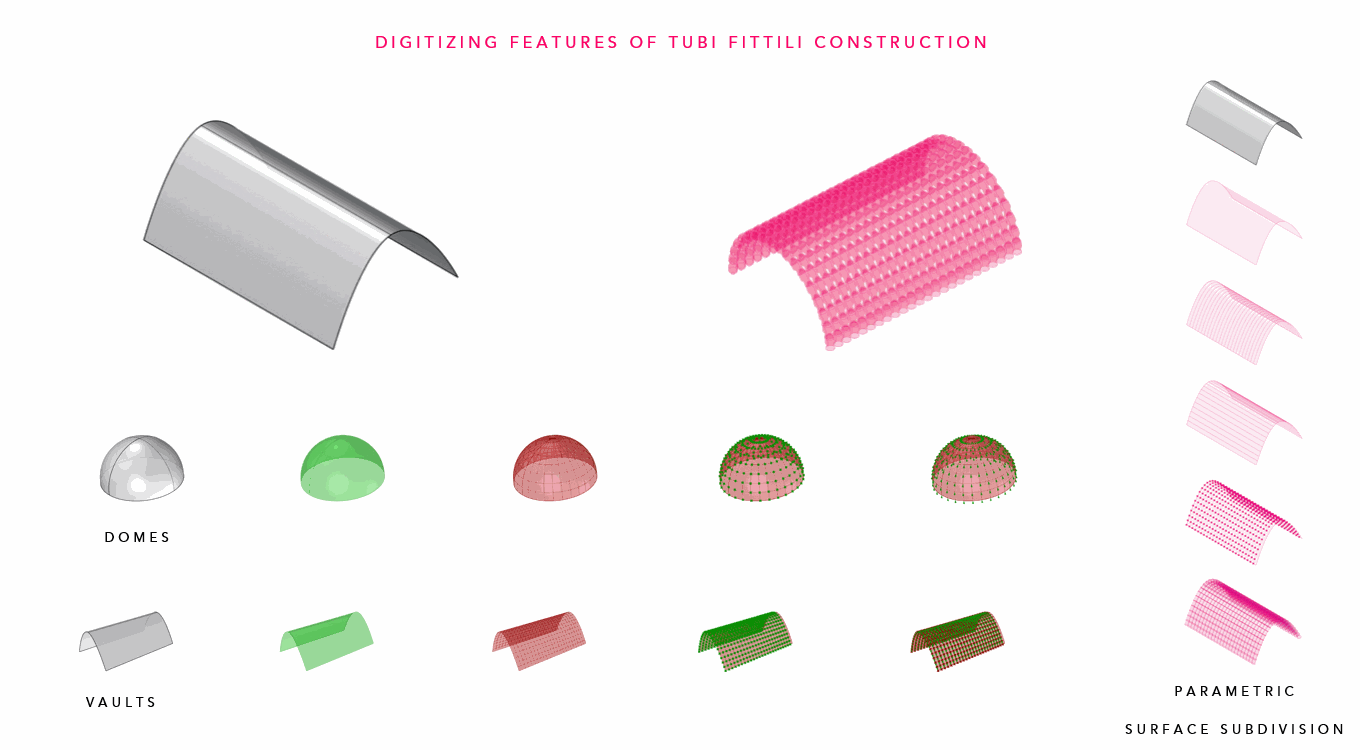
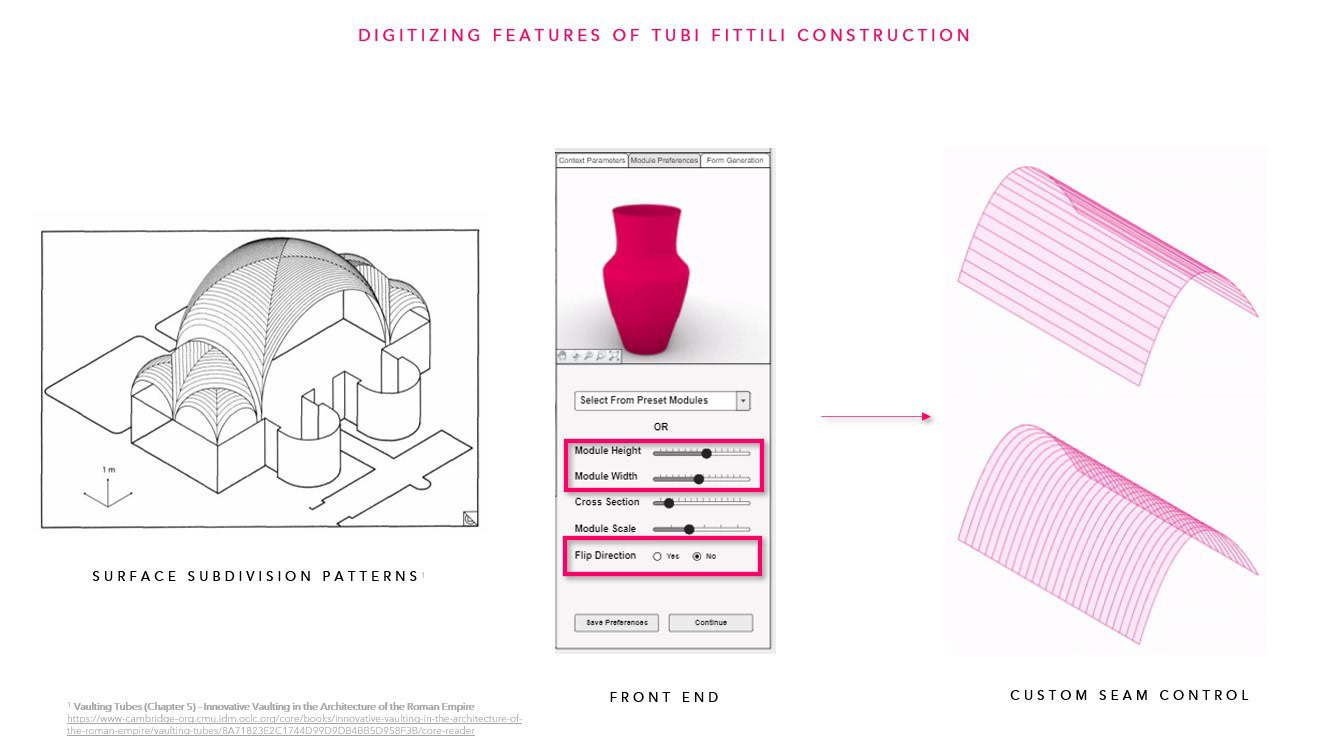
Specifying the type of structure might also be necessary as it might talk about how the structure is aggregated. In the case where the user wants to include radiation studies – specification of location is required.
While these design phases may seem linear in nature, one might always be able to go back and update previous preferences to analyze design variables and their effect on the form produced
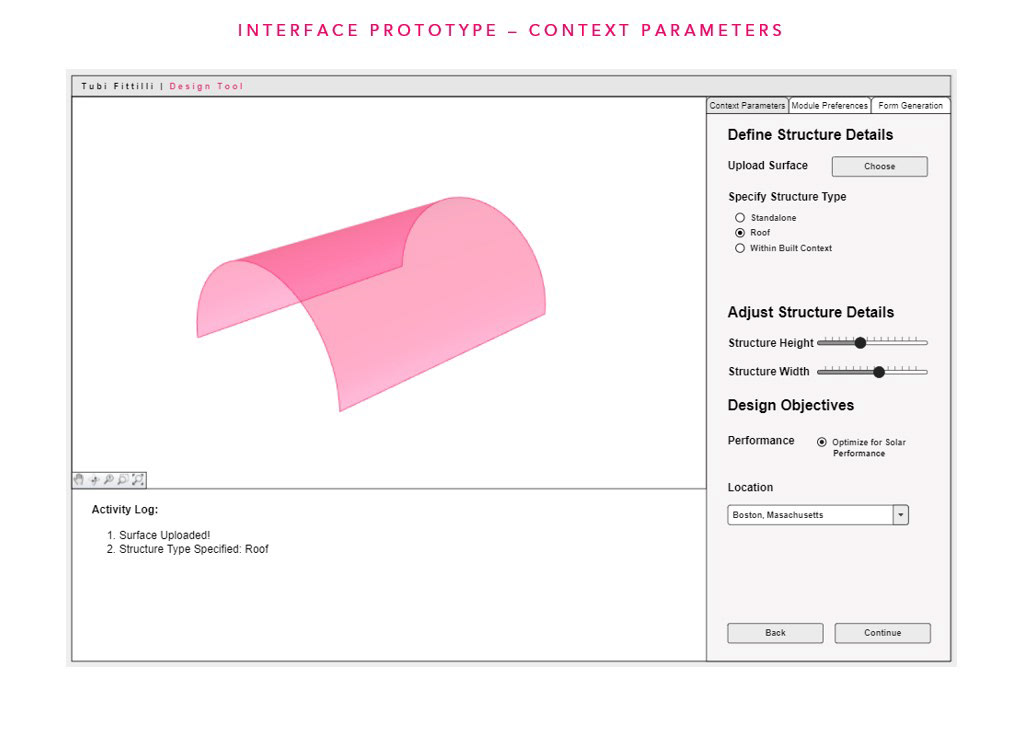
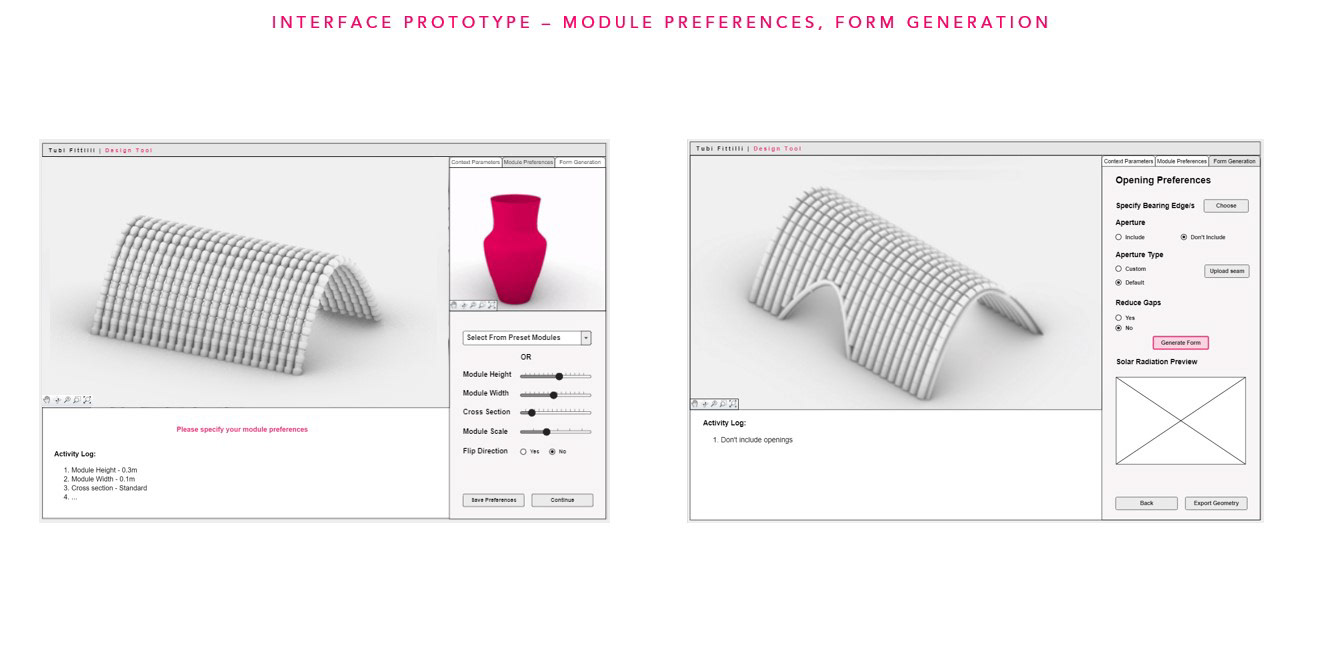
The results from my experiments worked fairly well where I tried working with simple domes and vaults, and also complex structures that are comprised of more than one drive surface. But the tool at it current stage takes a lot longer to process more complex surfaces.
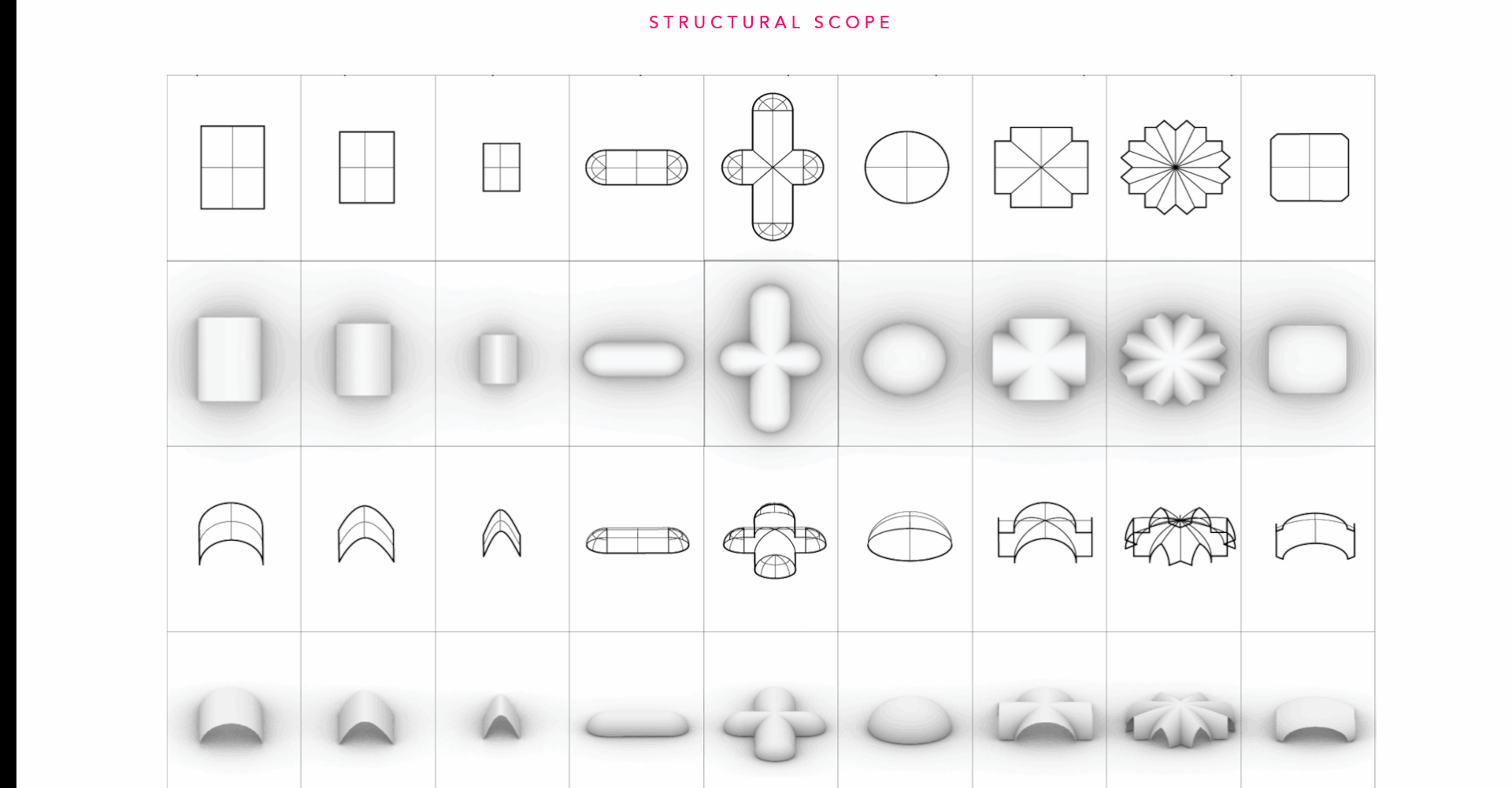
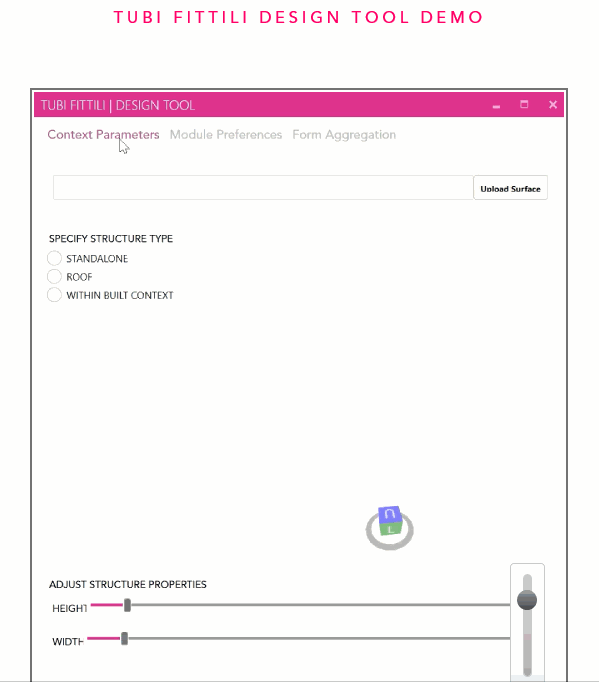
The next part of the project is the mixed reality assisted construction prototyping setup
Tubi fittili is Nonintuitive as compared to standardized construction and requires an added level of guidance while placing the blocks in position.
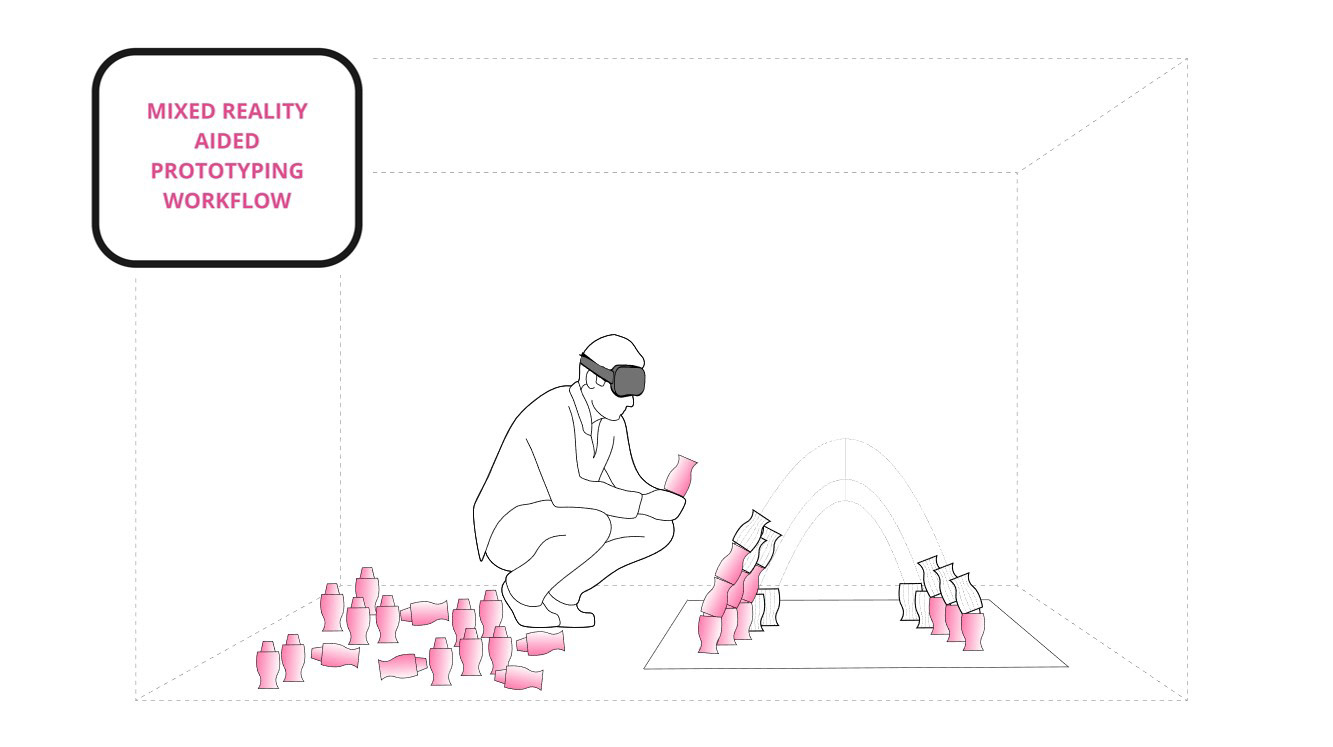
The attempt is to create a suggestive framework, that indicates the user about the precise placement of modules relative to one another. As seen in this video
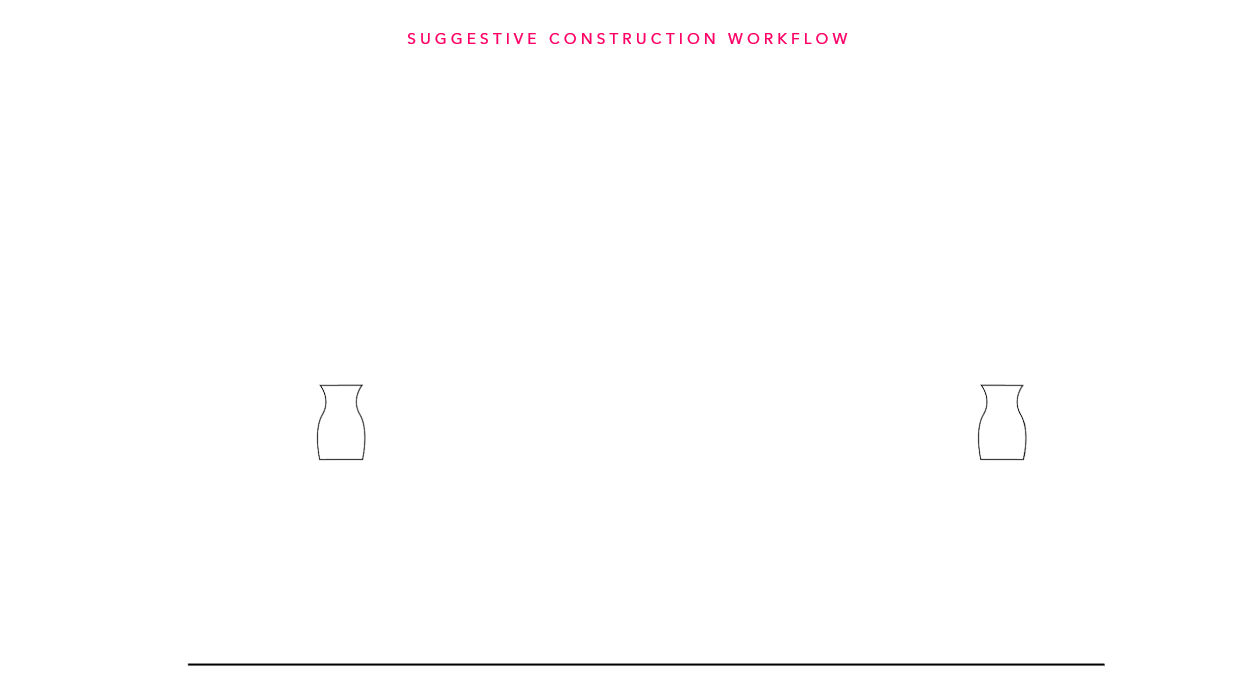
While working on this demo, a lot of challenges were seen which could be viewed as opportunities seen –
The user was prototyping a part of the design she made using the tool and decided to go against the suggested workflow because it did not seem to work very well with the structure they had envisioned – an irregular arch- which was also to challenge the design environment I had created.
Here the user takes the range of deflection of each pot as a complementary factor in the creation of the structure – while this approach may seem to work and seem better than the suggested workflow, in reality, when the pots are mortared in position – it would definitely require the user to place each pot in position - precisely.
So in my effort to unconceal this lesser-known, nonwestern building practice, I understand how the characteristics of tubi fittili construction can be digitized within a design and prototyping space and presented to a designer. In the process of working on this project, I always wondered how one could possibly build upon this pipeline, and scale-up workflows to be deployed on-site at relevant occasions?
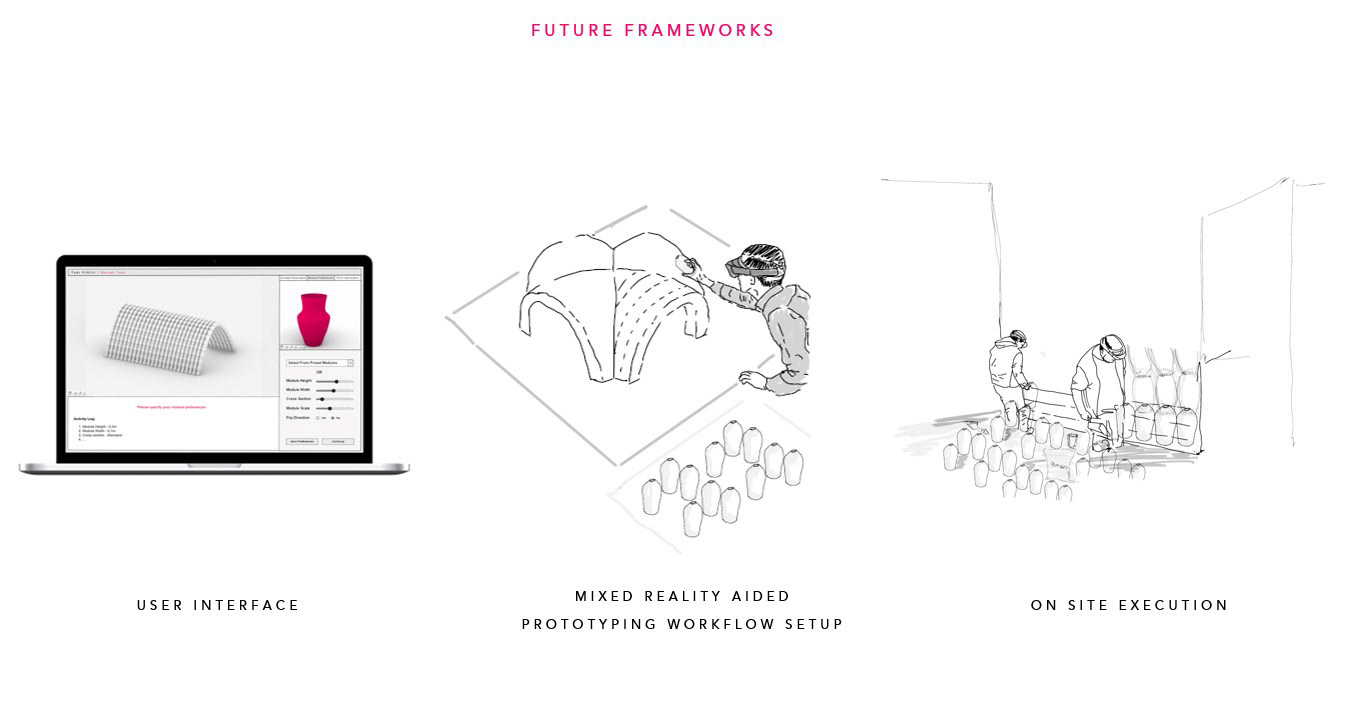
How do we as designers create more such frameworks to contribute towards preserving local wisdom, rebuild our knowledge base and generate new dialogues across disciplines and cultures? Because in the end, it is not just about this building practice that I'm looking at – there are so many communities waiting to be empowered and recognized.